私たちの強み
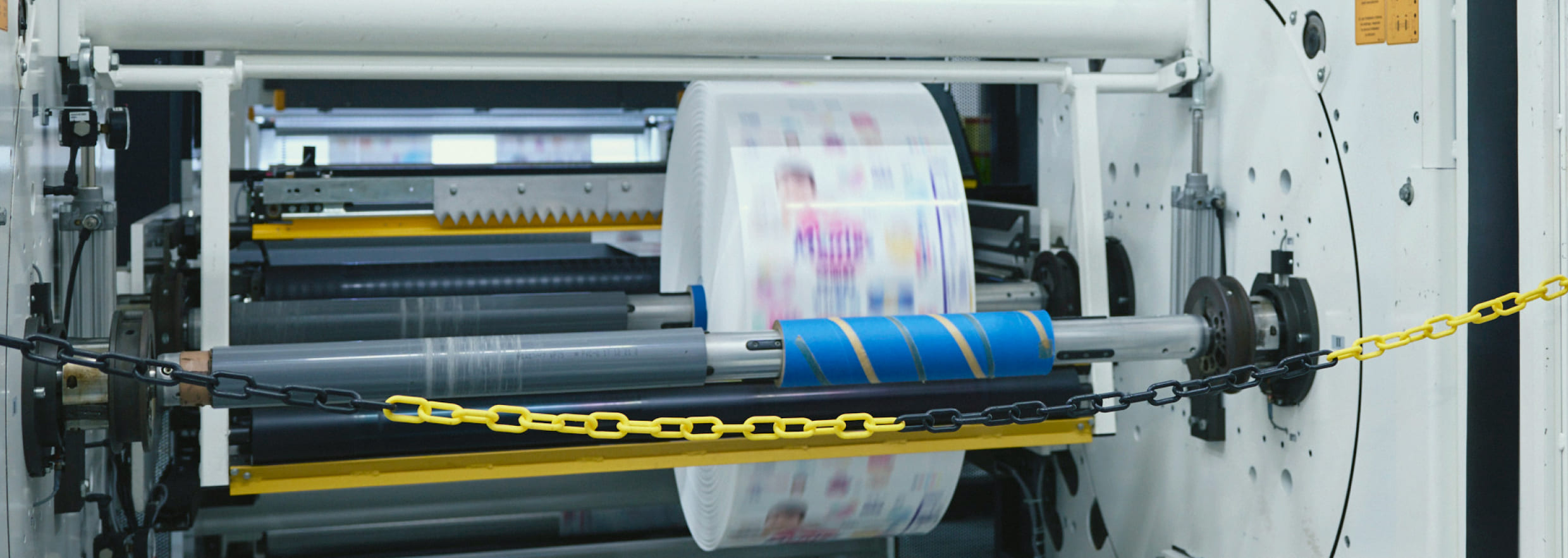
“一気通貫”の製造体制
大森化成は“ものづくり”と“ひとづくり”を事業活動の中心に置いています。一人ひとりの社員が複数の工程を経験し、製造の上流から下流まで緻密に連携しているため、一気通貫の高品質なものづくりが可能です。お客様からのご相談を受けて生産し、出荷するまでの各工程の仕事をご紹介いたします。
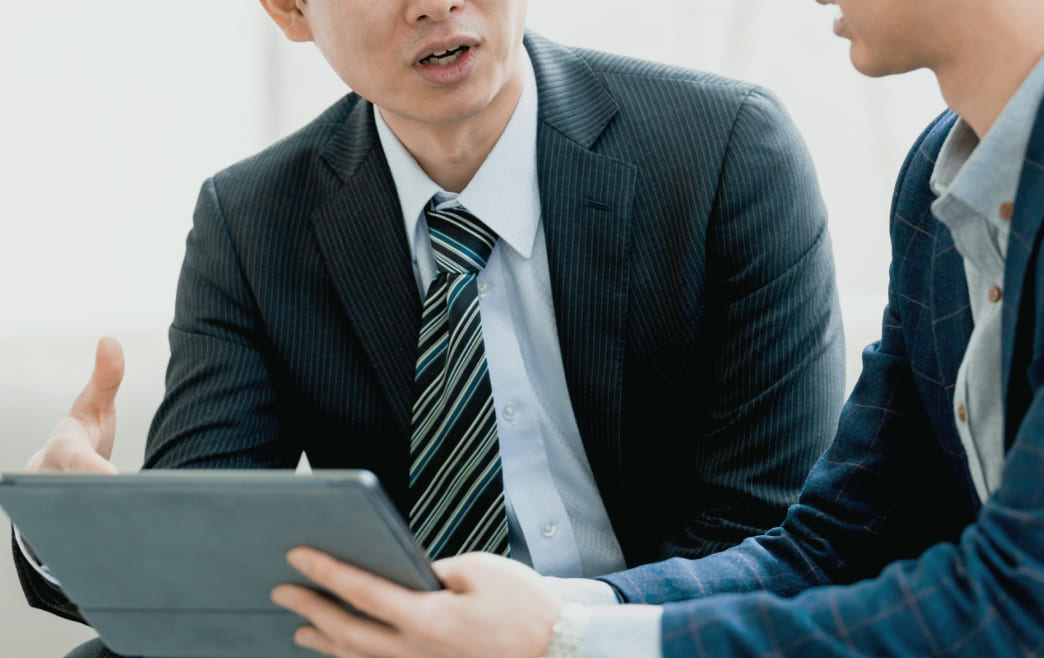
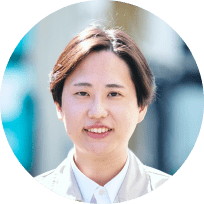
生産したパッケージの品質がそのまま大森化成への信頼につながるので、トラブルのないよう生産し納期に応えることを第一に考えています。時に納期を早くできないかというご相談もあるのですが、自信をもって規格を出せる品質に仕上げることを最優先にしたいと思っています。お客様からサンプル依頼があれば生産現場と一緒に考え、サンプル試作を出せる体制を整えています。今後も産業界の発展につながるものを作っていきたいですね。
年々高度な品質が求められるようになってきました。社会的な環境意識の高まりや、お客様の内包物(製品)の進化・高度化などが理由です。これまで継続して生産してきたフィルムでも、さらに高い規格で生産してほしいという要望もあります。大森化成は、お客様と一緒にパッケージを開発してきたものづくり会社です。お客様の用途をお聞きし、それに必要な機能を備えるパッケージを提案するのが喜びであり、使命だと思っています。
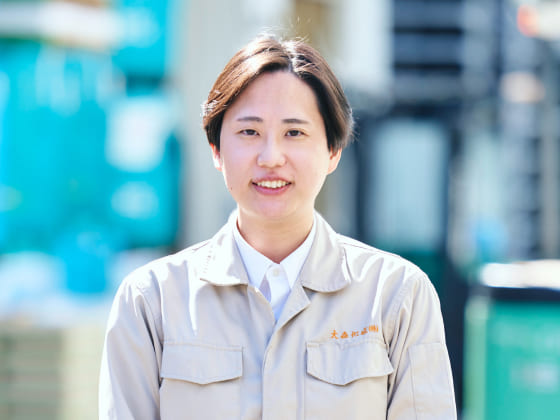
営業部
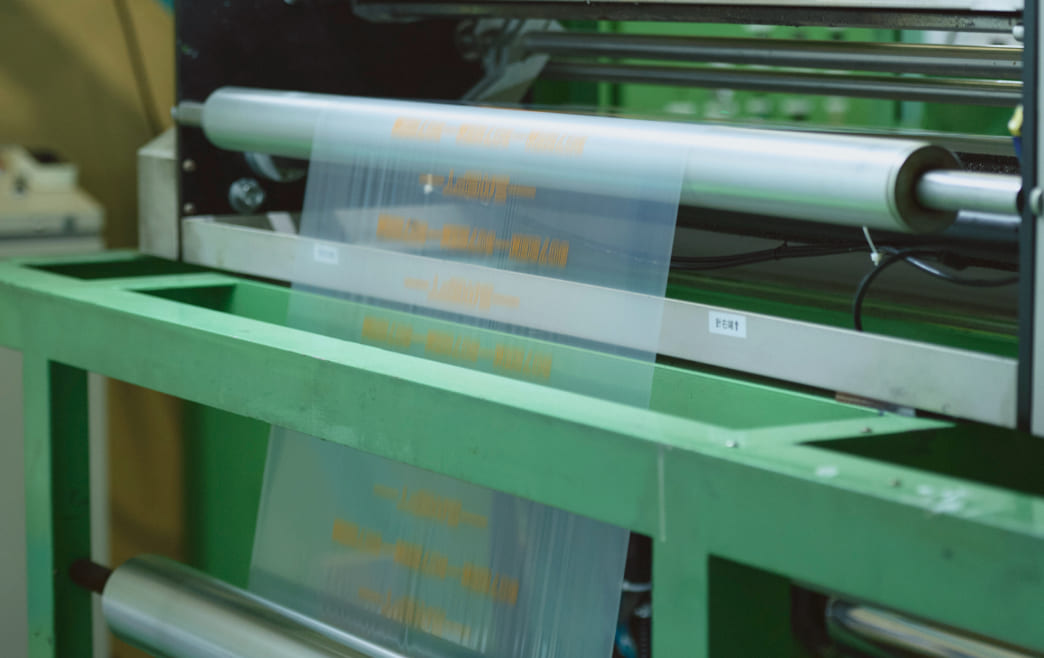
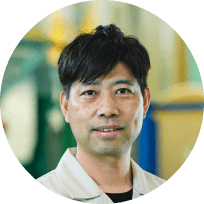
最初から思うような規格や品質に到達することはほとんどありません。何度も何度も試作を重ね、チャレンジの末にやっとお客様の要望を満たす規格を出すことができるのです。
当社ならではのスピード感のある判断力と実行力で、難しい試作でも形にしていくのが大森化成の強み。どうすればお客様に喜んでもらえるかを考えながら、各工程に関わる全員が協力して進めるからこそ、お客様の期待に応える製品開発ができるのだと思っています。
これからの時代は環境に配慮した原料でパッケージを作っていく必要があります。いかに環境負荷を少なくするかは、お客様にとっても重要なテーマです。大森化成は製造過程で原料のリユースやリサイクルにも力を入れて「エコ生産」に取り組んでいます。生産したフィルム自体も廃棄されないもの、再生しやすいものを作っていくのは私たちの命題。内容物と一緒に袋ごと溶かして使用できる特殊な「溶融袋」は、ゴミにならないパッケージとして注目されています。
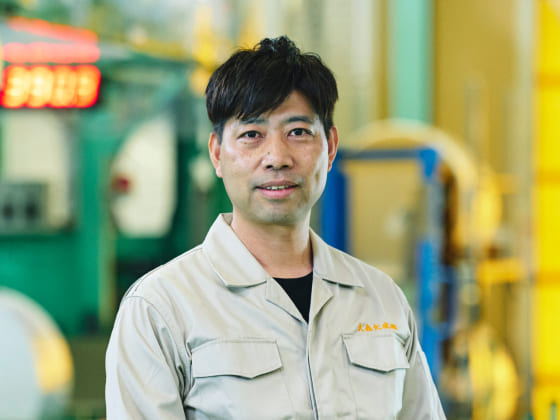
業務課
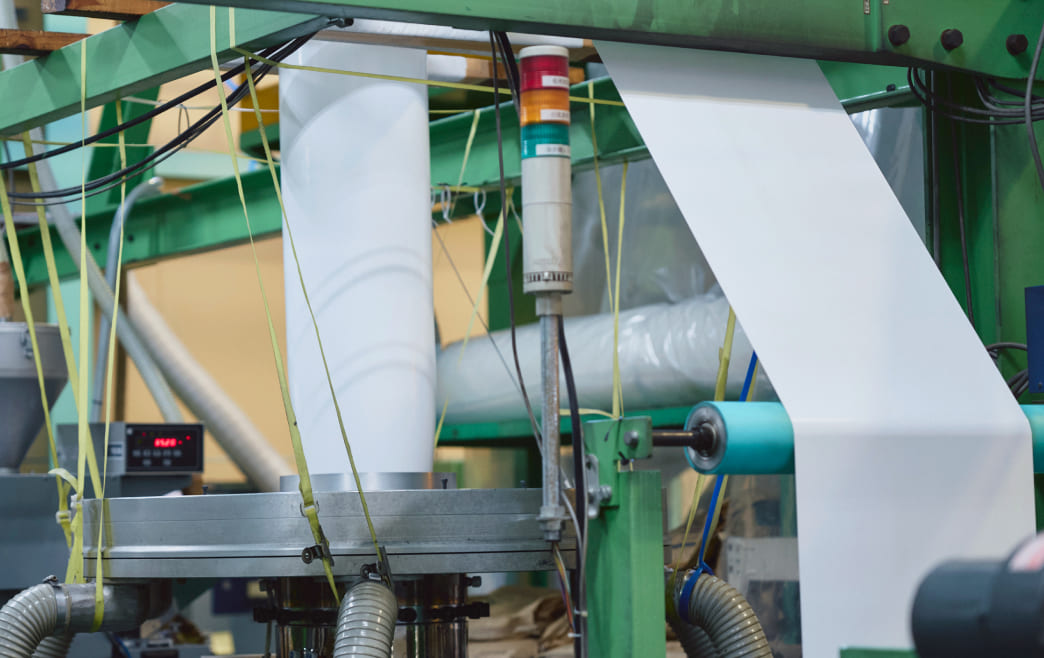
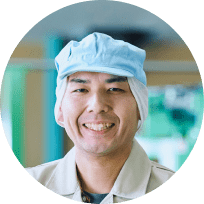
成膜の難しさは同じ原料で同じ形状のフィルムを作る場合でも、気温や気圧などの条件が違えば同じ規格にならないところです。基本的には機械に原料を入れれば作ってくれるのですが、機械任せにするのではなく、人間の目や感覚で労を惜しまず丁寧に調整していきます。巻き上がっているフィルムをチェックして、均一な規格になっているかを常に確認することがモットーです。シワにならず幅がバラつかないよう注意して仕上げていきます。
交代制で機械を稼働させているので、できるだけ生産ロスを出さないよう前後のオペレーターと綿密にコミュニケーションを取り、情報共有を行っています。ロスをできるだけ少なく生産する。その達成のために機械のトラブルやヒューマンエラーを少なくし、規格通りのフィルムを生産できるようチーム一丸となっています。まれに前回と条件が全く同じでも同じ規格が出せないこともあり、検証して原因を突き止めたときは「やった」という気持ちです。
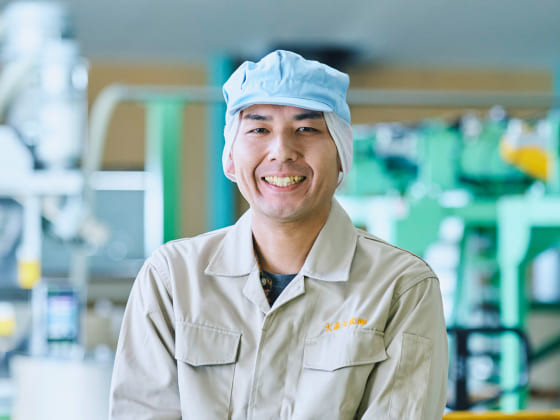
フィルム課
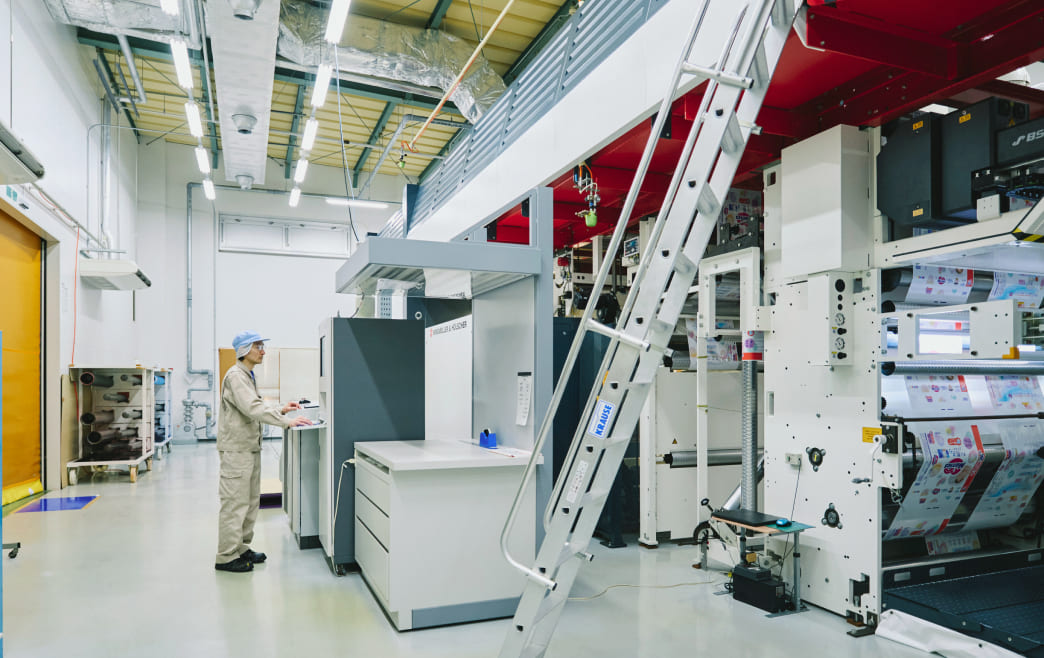
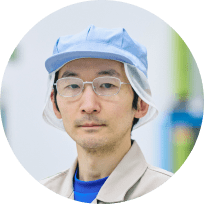
色の調整はある程度のスキルがないと難しいです。1日のうちでも朝の刷り出しは色が淡く、刷る回数を重ねると徐々にインクのノリが良くなり、濃くなっていきます。そんなとき、色の濃淡を目視で見極め、印圧を下げたりして色調を合わせます。
サンプルを刷って色出しをするのですが、印刷ロットを回すためにいかにサンプル刷りを少ない回数で調整できるかが勝負です。印刷スピードを上げるには、効率よく色調整をすることが欠かせません。
印刷機のポテンシャルはかなりあると思っています。現在は成膜したフィルムに転写を重ねて8色までの印刷が可能。特色の印刷でお客様の企業ロゴをはじめ、パッケージのデザインを規格通りに再現することができます。当社のフレキソ印刷機は転写する色がズレにくく、反転機がついているので、表面、裏面同時に印刷できるのが特徴です。
大手メーカーであるお客様からはパッケージ印刷を10年以上も継続して依頼されており、フィルム生産から一貫した体制で仕上げています。
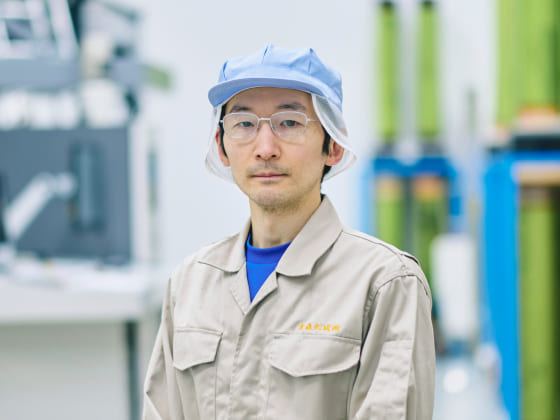
印刷課
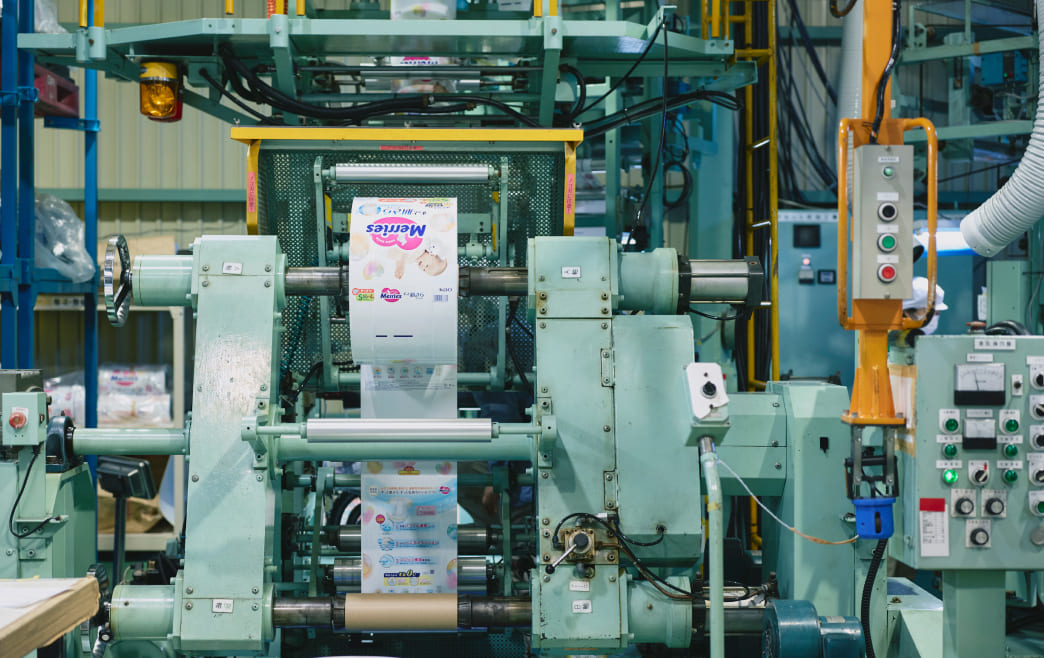
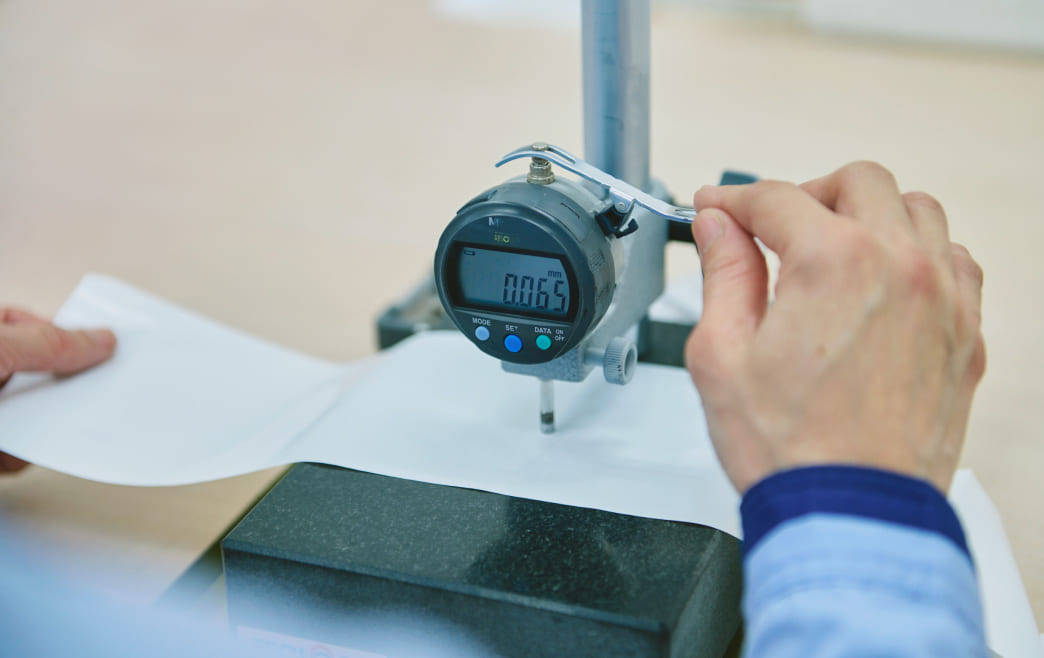
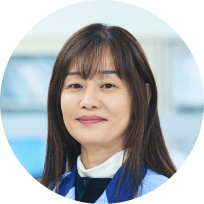
1日のうち朝、昼、夜で製品の仕上がり具合が変化するため、入念にチェックします。一人で見るのではなく、必ず複数人で厳しく検査するのがポイントです。
製品の規格が出ていない場合は、原因を突き止めるために成膜工程や印刷工程に行き、オペレーターと直接会話するようにしています。生産現場の意見を聞いたり、機械の特徴を聞いたり、「なぜこうなったのか」とコミュニケーションを重ねることが品質管理のうえで大切だと思っています。
検査といえば一人で黙々とチェックをしているように思われがちですが、大森化成の検査は違います。良いものを作るにはコミュニケーションが絶対に欠かせません。成膜の担当者や印刷の担当者と意見を交換し合い、「もう少し厚く」など規格の真ん中を目指して、部署を越えて連携することで製品の品質を高めています。
生産ロスを出す前に上流工程でチェックして食い止める。そうして良い製品を作るのがやりがいです。
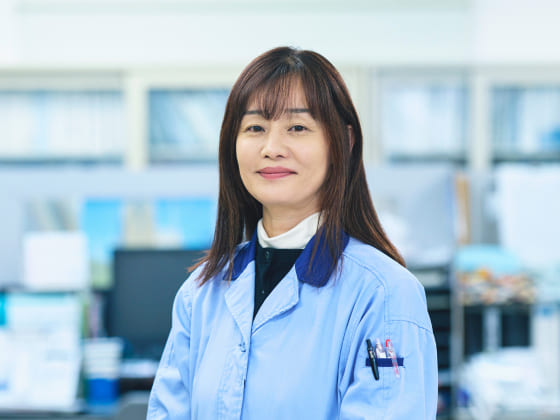
品質管理部
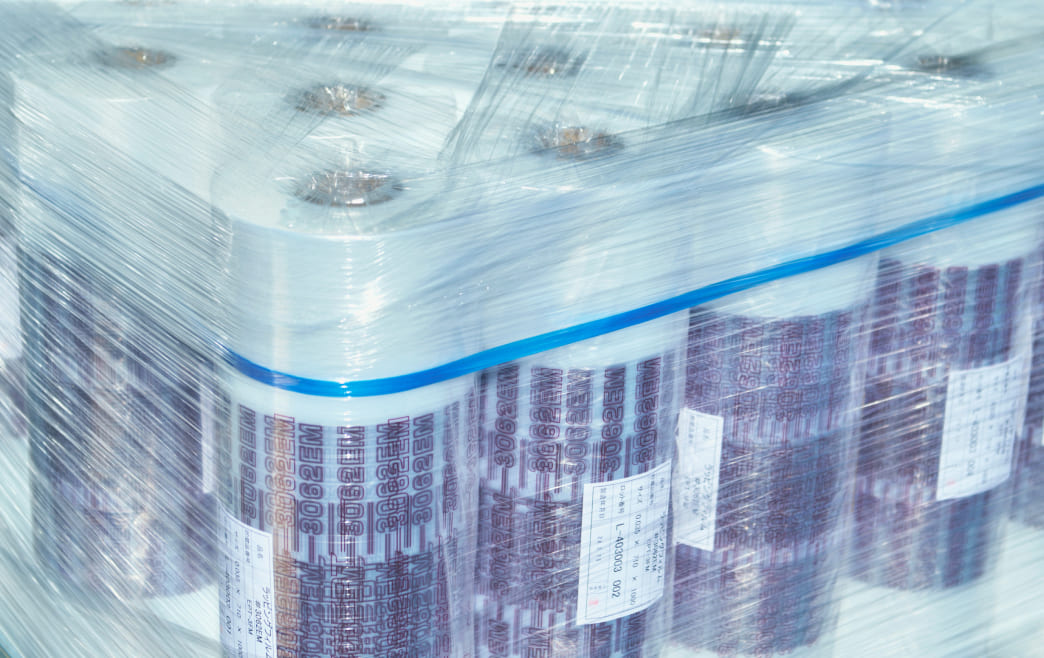
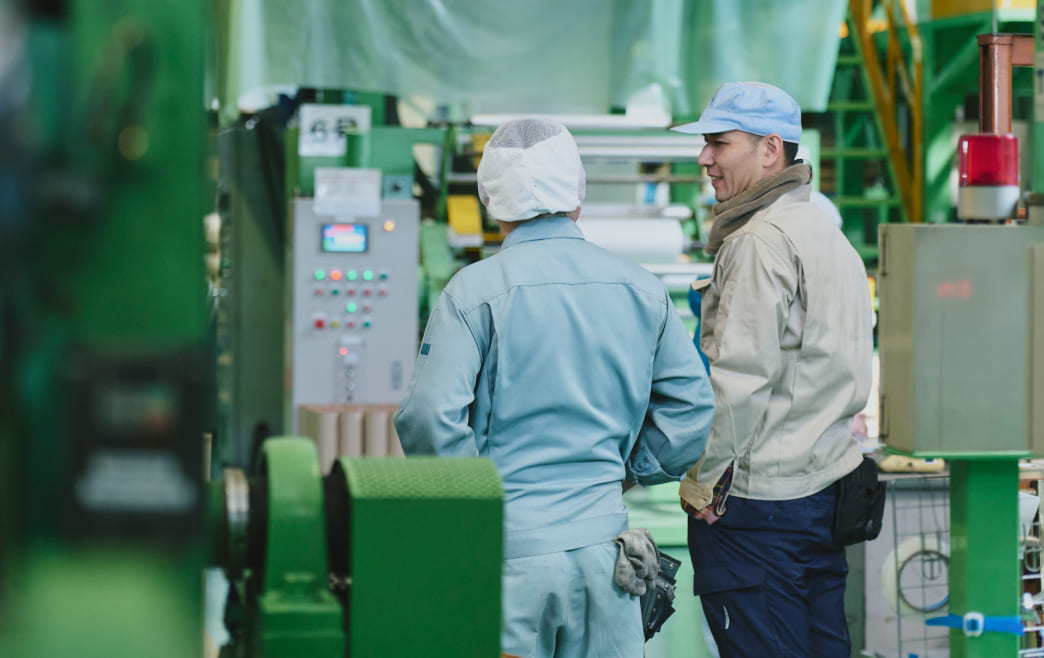